IQAX: Offering All-Inclusive Reefer Container Monitoring Solutions
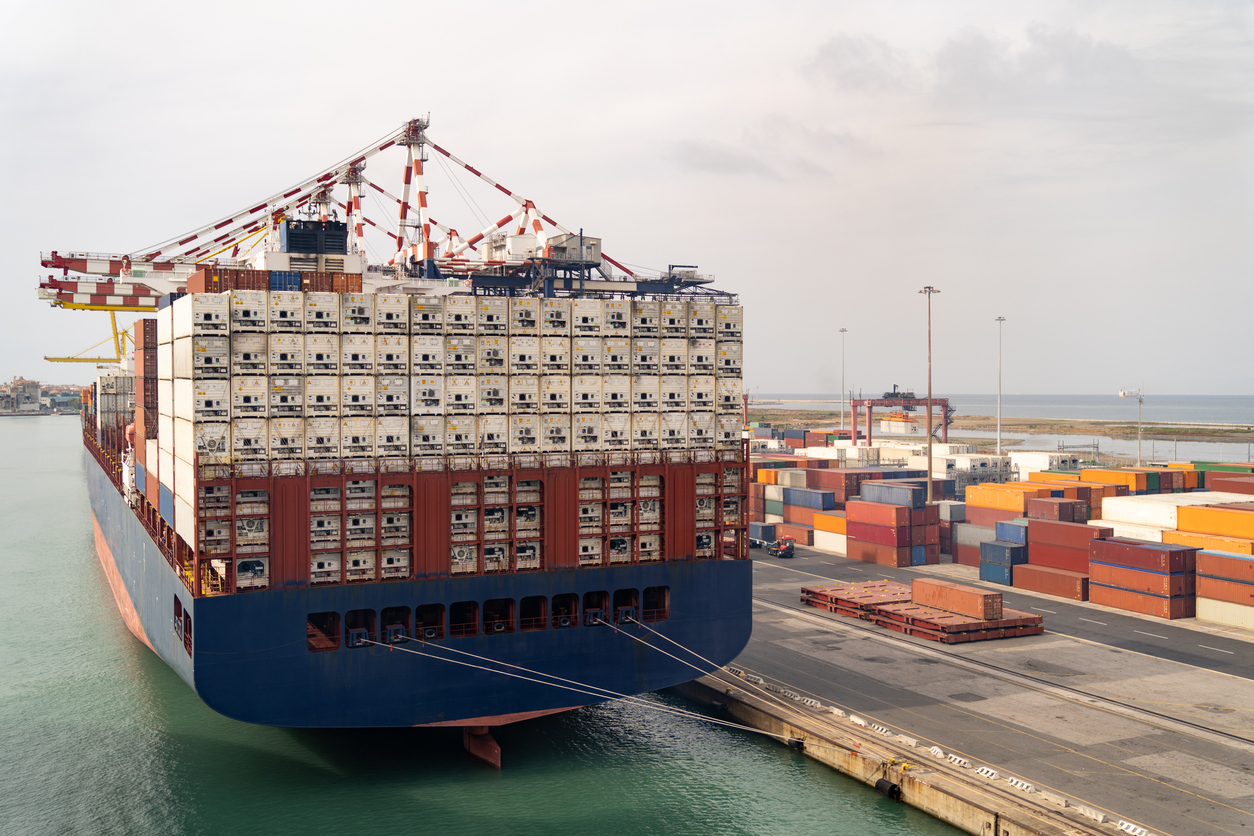
The expansion of international trade and the increasing demand for perishable goods worldwide have contributed to the significant growth of the reefer container market in the past few years. According to a recent report, the global reefer container market is expected to be worth USD 24.6 billion by 2030, growing at a CAGR of 6.1 percent during the forecast period 2025-2030. The demand for efficient and reliable reefer container monitoring platforms is more critical than ever. Ocean carriers can leverage these platforms to meet the increasing demand in the expanding cold chain market, ensuring the safe and efficient transport of perishable goods worldwide. IQAX has invested into BoxPlus Information Technology Company Ltd., a provider of IoT solutions, becoming a shareholder in the Shanghai-based developer of container shipping IoT devices and supporting the fast-growing reefer market with IBOX Reefer. IBOX Reefer combines IQAX’s innovative software capabilities with IoT devices and sensors developed by BoxPlus. This allows carriers to monitor temperature, humidity, oxygen and carbon dioxide levels and detect any deviations or abnormalities. |
|
By having this level of monitoring and control, ocean carriers can proactively manage and optimize their reefer containers, ensuring that the quality of the cargo is unaffected. Providing this accurate and timely information to their customers leads to enhanced customer service and improved trust and satisfaction. The monitoring platform helps carriers save time and labor costs with effective and efficient execution of pre-trip inspections (PTIs). To date, it has connected over 92,000 devices, covered more than 200 regions and successfully operated in over 11,000 city pairs.
It intelligently analyzes container usage, maintenance history and identifies damage to the reefer container. Ocean carriers can significantly reduce manual PTI checking workloads and expedite cargo distribution throughout operations.
Taking the increasing demand for service quality and streamlined operations into consideration, IBOX Reefer's smart PTI ensures machinery meets industry standards, analyses container usage and maintenance history and identifies damages. Its visual recognition capability significantly reduces manual PTI workload, expedites cargo distribution and is estimated to save carriers more than 70 percent of PTI costs per year.
Apart from Smart PTI, IBOX Reefer also offers two more capabilities including hot cargo detection, and failure component detection, which can help to identify cargo condition change impacts and reefer container failure problems. With failure component detection’s ability to offer comprehensive record of the container history increases the accuracy of reefer machine condition projection to lower the functional breakdown during the trip. The transparency of the container history that it provides clearly indicates the machinery performance of reefer box.
The hot stuffing detection’s AI model helps to identify the potential hot stuffing cases in advanced and enables users to send a push notification to customers to notify them. For example, the shipper who is shipping durian has no warehouse to pre-cool the cargo. They are doing hot-stuffing which manual defrost onboard the vessels or on the terminal must be performed every 3-6 hours until the cargo is on temperature. If the reefer container failed to pull down before loading, customer service is required to contact the shipper to sign a LOI. At the same time, the reefer machinery will be put under stress often with a malfunction as the result. This strain will decrease the efficiency of the container because the frequent defrost cycles make temperature control difficult which may result in poor quality of the product. That’s what hot stuffing detection’s AI model can mitigate.
Furthermore, the solution helps monitor the reefer around the clock and provides proactive notification if an exception is detected. For example, it gives a door open alert if the container door is opened during transit and has a route deviation alert, which notifies the carrier/cargo owner if the container deviates from the predefined trip plan. Carrier/cargo owner can keep track of unauthorized stops and events and minimize the risk and plan for the next leg.
IBOX Reefer’s device running frequency is update every 60 minutes and under the situation of this update frequency, it can work for more than 40 days without an external power supply with a rechargeable battery. It provides continuous coverage without draining battery power and helps carriers maintain the freshness and quality of temperature-sensitive goods while reducing food wastage. This aligns with ocean carriers' focus on reducing costs, enhancing cargo delivery, minimizing risk and improving environmental quality.
With its long-lasting battery life and continuous monitoring capabilities, IBOX Reefer not only meets industry standards but also aligns with carriers' goals of cost reduction, enhanced service quality, and environmental sustainability. By embracing such innovative solutions, ocean carriers can position themselves at the forefront of the expanding cold chain market, ensuring the seamless delivery of perishable goods while mitigating risks and optimizing resource utilization.
written by Logistics Tech Outlook